How can we present 2 years warranty?
As we are manufacturing brake system parts with over 40 years experience, we are precisely care about quality.
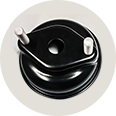
Electrostatic Powder Coating
We have fully automated powder coating system which utilized with GEMA equipment. At the coating line we are consuming Chemtall's surface treatment chemicals to ensure coating adhesion. Right after surface treatment we are consuming DUPONT's powder.
Each step of coating process is inspecting by quality department such as surface treatment chemical formula, Ph value, drying process, coating process, heat treatment process. We are also utilized with environmentally heating system which uses BIO FUEL.
Spring Manufacturing
Spring is the one of the most important part in brake chambers. We fully equipped as a professional spring manufacturer which includes:
- Spring Coiling Machine - Stress Relieving Oven - Surface Crack Testing - Shot Peening - First Loading - Coating
It's also very imported to choose right spring wire. We are cooperating with IST in UK about design, test and standards and using imported spring wire for all of our chambers.

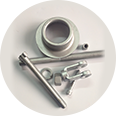
Dacromet Plating
DACROMET is a US based brand which is providing high quality environmental coating raw materials. It mainly used in auto industry to coat all kind of bolts, nuts, washers, metal plates etc...
The parts which we can't do powder coating in local, we are doing DACROMET plating. It's corrosion resistance is very high as it's can durable till 500 hours in salt spray test.
Aluminum Tray
Aluminum tray used inside the D/D brake chambers as spring bedding and push disc which is not harmful for diaphragm. It`s working always under the high pressure and it`s easily break off if the quality not good. Because most of the companies are not doing well, it's also sales separately in aftermarket.
Our aluminum tray has a special raw material which fits European standards and there is neither crack inside nor surface.
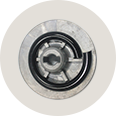
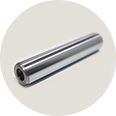
Chrome Plating
Inner rod which transfer brake force from spring to push rod has plated with hard chrome. It's smoothness surface will let it work into aluminum body without any scratch and deformation.
Inner rod has very critical part inside the brake chamber and work in very tight area. If it's leak will cause fatal brake failure and vehicle will stuck by spring brake.
Push Rod
In order to transmit right braking force, push rod metal plate's diameter is very important. Following to EU standards, each type of brake chambers has to obtain specific brake force. In market, has too many brake chambers with wrong size and thickness metal plate.
If the metal place is thin, under high pressure it'll deform and wear the diaphragm. Our metal plates are 6mm and it has been pass from machining process to not wear diaphragm.
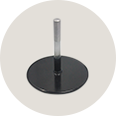
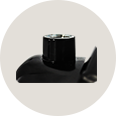
Projection Welding
Our bottom covers on service brake chambers has one sometimes two welded nuts on it. Welding method is very important to prevent leakage and being durable.
Instead of MIG and TIG welding, it's looks smooth and it's much durable. In case of any kind of impact, projection welding will never break off.
Durable Diaphragm
Our diaphragms are made with special formulation and inner fabric is special made. From the manufacturing method to choosing raw materials we are manufacturing our membranes with high meticulously.
Diaphragm durability reached 1,500,000 cycles at fatigue test in brake chamber. We it has been passed from Ozone ( Aging Test ), High and Low Temperature Test, Hardness and tensile test.
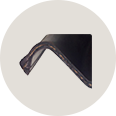